These pieces represent only a few of
the large number of knives, tools and weapons I have
made since the late 1970's. This has included
everything from small 'hide out' knives to full sized
'bastard' swords - working tools to combat blades.
From the very first, my interest has been the blade as
cutting edge - not so much as a decorative object.
• I have remained most interested in the wide
possibilities of aggressively forged blade
shapes. (Rather than the more limited 'straight ground
from bar' profiles so common to 'knife makers')
• Although I have worked extensively with layered
steels, my work centres on the more dramatic potentials
of Norse inspired, multiple twisted bar, 'Pattern
Welding'.
• Even when working with more conventional flat stack
('Damascus'), I prefer the randomly distorted lines
created buy aggressively hand hammered billets.
• To maintain durable cutting edges, most layered steel
billets are then forged welded to a solid carbon steel
core (creating a more functional hard edge).
• Many knives feature 'one piece' construction, as I
have less interest in the 'knife as jewellery' aspect
seen in much contemporary knife making.
Objects are shown from most recent to
earliest work.
Samples of Past Work
are also seen on
'Custom BLADESMITHING'

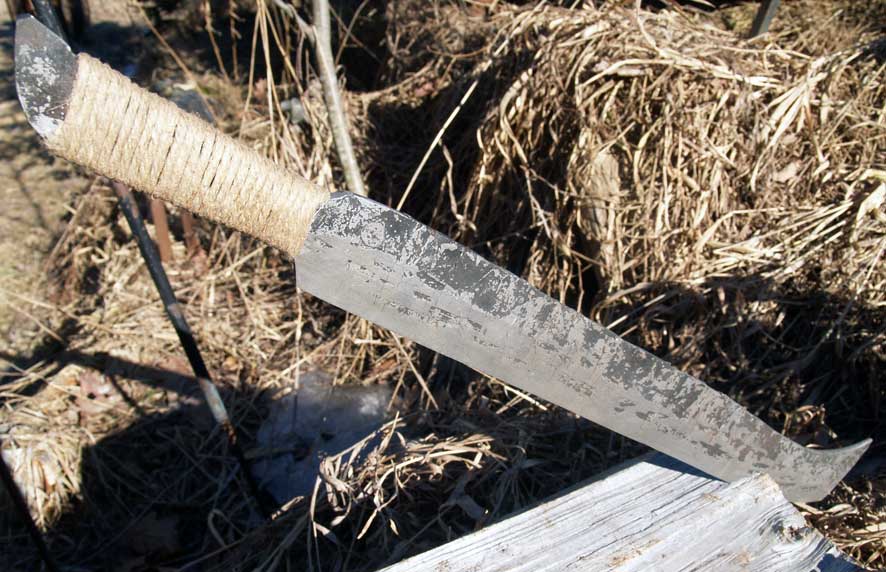
|
'Darkness
Take You'
Summer 2015
water hardened mild steel with steel inlay
hemp cord wrap
'Darkness Take You' was another attempt to
have some fun with the mental image of clumsy Orcs,
toiling away in the dankness of Saurman's Isengard.
(see 'Orc Knife', further down here)
The blade is deliberately roughly forged and only
semi-polished, ground to a 'display' thinness on the
edge.
It also uses a special 'inlay' technique I have been
experimenting with. Close examination will pick out
the text 'Good Day to Die' and 'Darkness Take You' -
in the language and runes used by the Uruk-Hai.
total 65 cm / 25 1/2 inches
blade 53 x 5 x .6 cm / 21x 2 x 3/16 inches
weight is 1100 gm / 38 oz
'Darkness Take You' was purchased in 2019 for
use in a current television production.
|
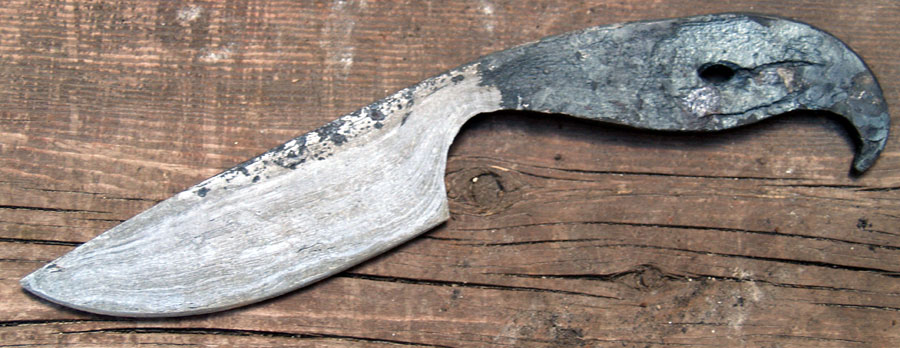
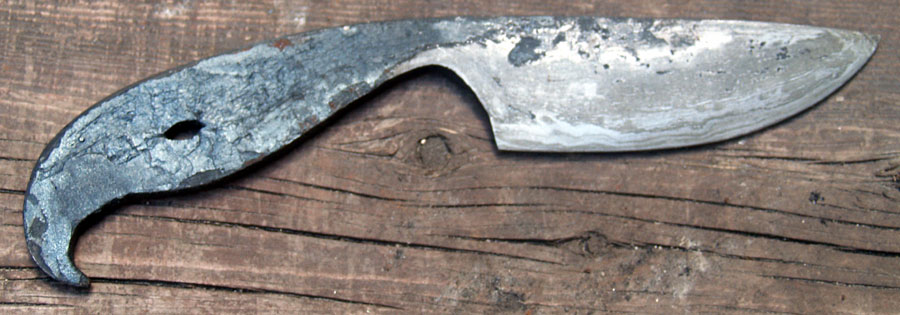
|
'Recycled'
2013
antique wrought iron
Before the modern age, iron was valuable, just as a
raw material. Old objects were commonly returned to
the blacksmith to be 'recycled' into new objects. I
had this small piece of scrap wrought iron, most
likely originally a piece of hinge strap or wagon
fitting. There was already a hole punched into one
end of the bar. I chose to re-forge the bar, leaving
the now distorted hole open. You can also see
several shear line cracks from imperfections in the
old metal, which I chose not to re-weld
closed. Loosely, the shape of this smaller
knife was inspired by my earlier work with one piece
kitchen knives.
Once polished, the blade surface was lightly etched.
The resulting pattern is created by slight
variations in carbon content within the original
wrought iron.
'Recycled' was purchased in 2019 for use in a
current television production.
|
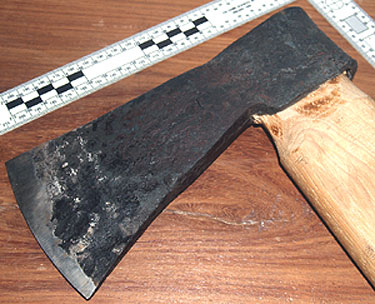
Finished Replica
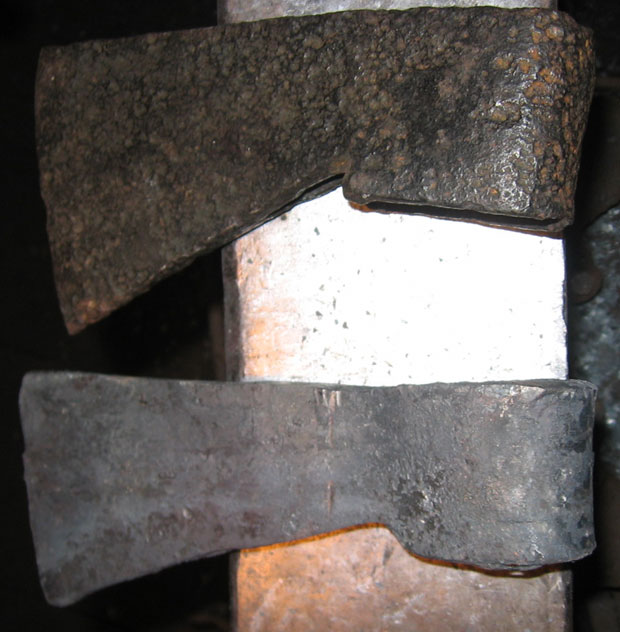
Comparison with Artifact
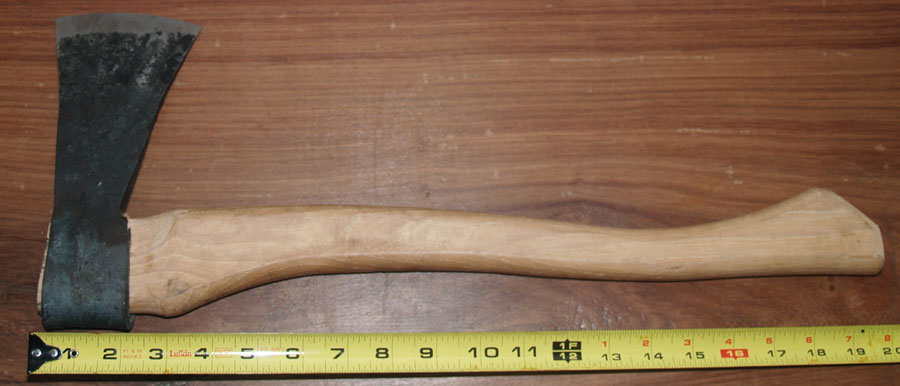
Full view with Handle
|
French Trade
Axe
2013
bloomery iron with inset carbon steel edge
modern (commercial) ash handle
$ 800 - this item available
One of the few actual artifacts I have in my
collection is a French Trade Axe. It is of the
'Biscayne' pattern, a type made specifically for the
Fur Trade. The object was found near Angus Ontario,
not far from the Nottawasaga River - the route from
Lake Ontario north towards Ste Marie Amoung the
Hurons. This pegs the earliest deposit date to about
1600 +. This type of axe stopped manufacture about
1760, so the most recent deposit date is not likely
beyond the late 1780's.
I decided to make a replica of the artifact, using
my own bloomery iron. This would match the original
metal, the forging processes, as well as the profile
of the axe.
In the end I had a bit less material to start with
than in the original, and my forged shape is not
quite identical to to artifact.
Finished dimensions:
head weight = 1050 gm
width at edge = 9.5 cm
total length = 20 cm
thickness at eye = 2 cm
width of eye = 5 cm
handle length = 51 cm
|
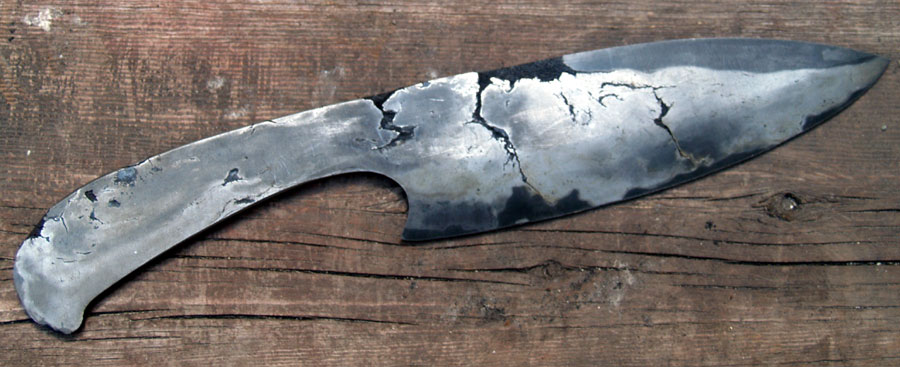 |
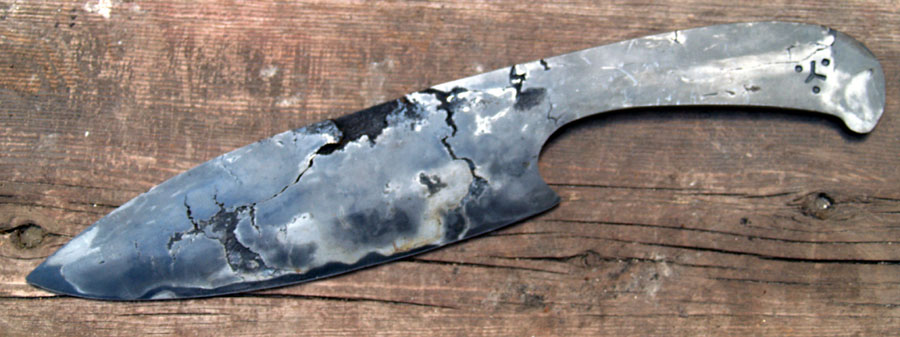
Hector's Bane : Finished - with etched
surfaces |
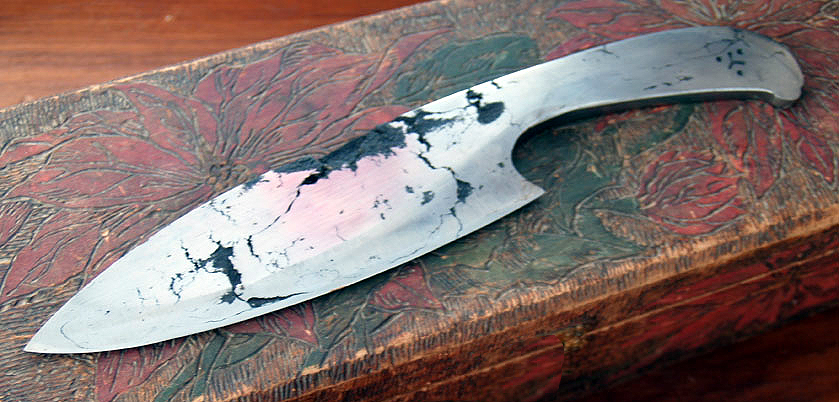
Hector's Bane : with original polished
surface |
|
'Hector's Bane'
Spring 2012
bloomery iron /
carbon steel core
$ 1000 - this item available
'Hector's Bane' shows a
combination of influences:
The unique nature of bloomery iron is featured by
deliberately allowing the natural flaws of a raw
bloom to remain. This has been emphisized by
etching the finished surface, the mottled greys
indicating variations in carbon content within the
material.
To create an effective cutting edge, the two half
pieces of one bloom have been forge welded on to a
hard carbon steel core.
The blade shape was inspired by ancient Greek
*bronze* knives.
After some consideration, the polished blade was
lightly etched. This resulted in a 'fog'
colouration over the surface, a result of the
variations in carbon content within the original
bloom.
26 x 4.5 x .7 cm overall / blade 16 cm
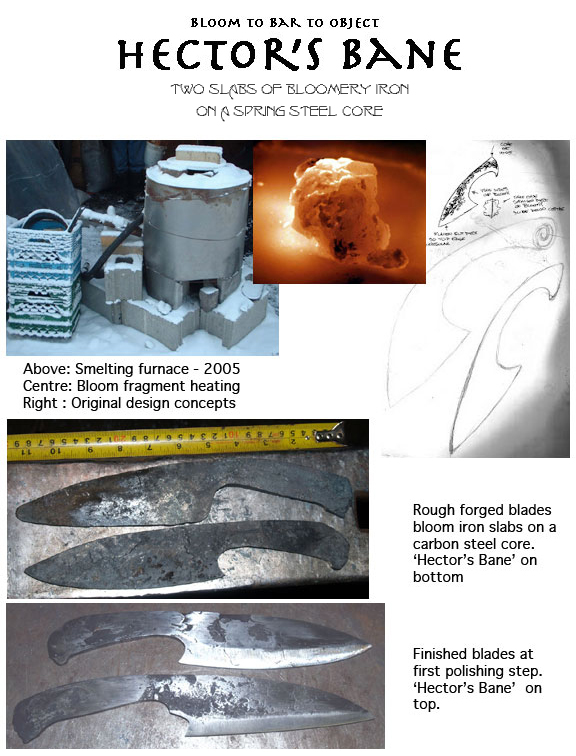
|
|
|
'Gull Wing' Axe, from
Bayeux Tapestry
mild steel with spring steel core
|
Wide Adze, from
Mastermyr Tools
mild steel with lap welded carbon steel
edge
|
|
Norse Ship
Building Tools
Spring 2008
for Parks Canada
In 2008 I was approached by Parks Canada to make a
complete set of Norse building tools for the living
history program at L'Anse aux Meadows NHSC. (I have
had a long association with this site and the Norse Encampment
program.) I was able to undertake additional
research in Denmark into historic prototypes.
A fuller description of this
project, and the tools created, is available HERE
|
|
Norse Heavy Tool Knife
Spring 2007
private
commission
The blade is a seax - here with
more of a lift and curve to the point. The overall
length of the blade is a bit over six inches At
its widest (just back of the false edge) the blade
is roughly 1 1/4 inch wide.
The blade is made up of 209 layers. The starting
block was 13 layers : M/LM/L/M/L/M/H/M/L/M/L/M/L/M
M = 1018 mild steel at 1/8" L = L6 alloy (.5
nickel and .5 carbon) at 1/16" H = 1095 carbon
steel at 3/16" The overall carbon content is
lower, with the bulk of the material being
supplied by the mild steel. The inclusion of L6 is
to mimic meteoric iron. This pile was welded and
folded in three for a billet at 52 layers. That
billet was drawn to a bar, with a third twisted
right, a third twisted left. The last third was
flattened and pulled out to twice that length,
then welded to a second core of high carbon steel.
The resulting bar was turned on its edge, and the
two twisted segments welded into the final billet.
This billet at 209 layers was forged out into the
blade. The finished blade is ground back at the
edge to expose this high carbon steel cutting
edge. This edge is hardened a bit more than normal
for a plain mono block knife, as the layered back
adds the required flexibility for the final blade.
The hilt is a natural piece of caribou antler.
The wire wrap is a feature the customer requested.
I drilled two small holes that the wire ends tuck
into, then the strands were soldered together at
top and bottom.
|
|
Pattern Welded Norse Seax
Spring 2007
private commission
The billet for this blade is primarily mix of
mild steel and a low nickel alloy called L6, along
with a layer of high carbon steel. The L6
simulates the use of meteor material in my
historic blades. (L6 is .5 % nickel and a middle
level .5% carbon - meteorites are closer to 5 %
Ni, but with no carbon). The initial stacks were
at 13 layers, these have been welded and folded to
four to give a 52 layer bar.
Part of that bar is drawn and cut in two. A piece
of high carbon steel is stacked between these and
the whole welded to form the cutting edge (at 105
layers) When forged to a blade and polished, this
hard carbon steel is exposed to form a durable
cutting edge.
Next the remainder of each billet was pulled to a
long octagon and twisted, just enough for two
rods. These were then squared and welded to the
prepared cutting edges. This gives a total count
of 209.
The blade was hilted with a length of natural
caribou antler. This was carved using Norse
patterns by another artist.
|
|
Pattern Welded Sgian Dubh
Spring 2006
private commission
This is a custom knife created for a customer
who wanted to mark his upcoming wedding with a
distinctive heirloom object.
The knife has a 5 1/2 inch long pattern welded
blade in a semi drop point style. The hilt is bog
oak - in this case oak recovered from an original
Roman era timber dock at the city of London, about
2000 years old. (What the English supplier told me
was the source.) It bears Celtic knotwork carving
on the right (out from leg) side and the owners
name and wedding date on the inner.
The blade is formed of a total of four core rods -
each at about 40 layers.
I started with a stack of 9 plates, then welded
and folded in four. The starting stack was
composed of mild steel / L6 alloy / wrought iron /
high carbon tool steel. The sequence was
M/I/M/L/H/L/M/I/M. This block was drawn and half
was twisted. This section with the right and left
twist was then cut and forms the two core rods
along the back of the blade. The remaining half of
the block was drawn out and cut in two. These
pieces were then welded to another piece of carbon
steel. When I count the layers (I include all four
bars) the total layer count is 158. The decorative
material is ground back to expose that hard carbon
steel cutting edge.
This was a fairly complex project. The creation of
the pattern welded billet was the most straight
forward part, but is always quite time consuming.
The bog oak proved quite difficult to get. This
material is quite hard, working almost like copper
metal. The surface carving was done with burrs on
a rotary shaft.
|
|
'Rivendale'
Fall 2004
sold to private collection
This is just one of a number of potential blade
profiles I had designed for a customer in late 2003.
The project involved creating a striking letter
opener using the pattern welding technique. This
particular profile, I had thought the most pleasing
of the lot, was not the one the customer selected in
the end. Latter (early 2004) I decided to make up a
small billet into this blade. In keeping with its
function as a letter opener, it has no carbon steel
core and is only sharpened at the very tip. |
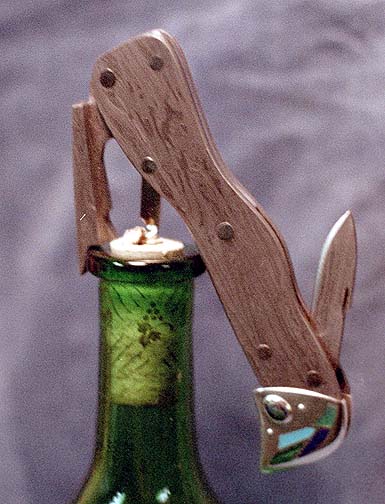 |
|
|
Shown in Use
|
Detail of the Layered
Pattern
|
Overall View
|
Layered Steel Opener
private commission
This unusual piece - a Layered Steel Bottle
Opener , was ordered by a customer as a
special gift for a friend. It follows the form and
function of a wine bottle opener - cork screw and
foil cutter. I worked together with silver smith Brenda Roy -
who created the silver bolster block inlayed with
semi precious stones. Overall the piece has an Art
Nouveau feel in terms of colour and line.
Completed in December of 2003.
|
'Possibilities of Damascus'
sold to private collection
Left side view |
|
|
Right side view |
'Possibilities of Damascus'
was created for the exhibit 'Traditions &
Innovations' in 2003.
The billet it was forged from was actually made up
several years earlier. This was a practice bar to
show the effects of a number of possible surface
effects on an even, high count, layered stack.
Again I used the heavy one piece blade and handle
style that I like so much.
|
'Orc Knife'
sold to private collection
Orc Knife was a piece done at the very end
of 2002, a couple of days after I had seen 'The
Two Towers'. It was an experiment in a number of
different ways. First - I had looked at the
production designs used for Jackson's 'Lord of the
Rings', and had tried to work in a similar style.
Second - I had used the air hammer for about 90%
of the forging, giving me good practice in shape
generation on that tool. Third - this object was
offered on sale over Ebay, my first experiment
with that venue.
A copy of the original Ebay listing can be
seen HERE.
This includes more details on the blade, the
design and some detailed images.
|
'Sword of
Heroes'
sold to private collection
Right side view |
|
|
Left side view |
'Sword of Heroes' is a
Pattern Welded Short Sword produced in early
winter of 2000.
This blade formed the centre piece of a short
television segment that originally appeared on
'Discovery.ca' in November 2000. This featurette
was produced by the Royal Ontario Museum, as
part of their continuing effort to relate their
collection to the work of artisans employing
traditional techniques.
More detail about the sword, with
production notes and close up views, is
available HERE
|
|